Intelligent control system
Provides recommendations regarding control of the process in the most efficient way. Increases equipment reliability.
Benefits
- Doesn’t require additional costs for the purchase of the third-party licensed software
- Built on the open source code
- Easily integrated into the existing IT-infrastructure of the plant
- Rolled out quickly in accordance with your requirements
- Has its own AWS interface or a possibility to output the results in your systems
What Datana Smart can offer
Operating procedure
Datana Smart
Receiving of the initial data
Data (readings) acquisition and processing online
Mathematic simulation
Machine model learning (ML) in combination with physical and chemical models builds a process of the work control of the machine
Recommendation feature
Recommendations on the process control
Solutions
Monitoring of ladle lining condition
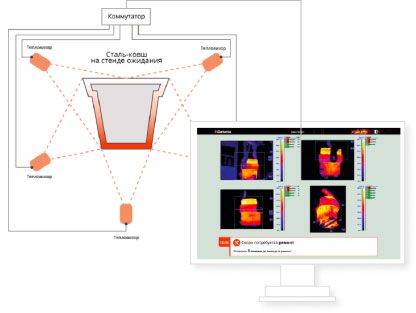
Range of issues
Occurrence of emergency situations as consequence of the ladles burn-through.
Solution
Development and implementation of the technical solutions and mathematical model, which identifies in the data patterns that are distinctive for the pre-emergency state of the lining (thermal anomalies of emergency areas). It predicts the remaining lifetime (providing recommendations on the schedule for the withdrawal of steel ladles for maintenance)
- Elimination of the unreasonable ladle decommissioning
- Reduction of financial costs for the emergency situations elimination, which are connected with the destruction of the ladle lining
- Reduction of metal loss
Optimization of the decarburization process at the vacuum degasser
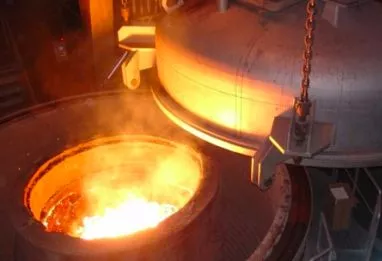
Range of issues
High content of the carbon in steel after finishing steel processing at the vacuum degasser. Significant influence of human factor on the decarburization process
Solution
Development and implementation of the solution with application of physical-chemical model of the decarburization process, which ensures providing recommendations in real time on the duration of the blowing of steel with oxygen in order to achieve required carbon amount and steel oxidation
- Increased metal quality
- Decreased duration of vacuum degassing treatment
- Decreased oxidizers consumption
Ferroalloys consumption optimization
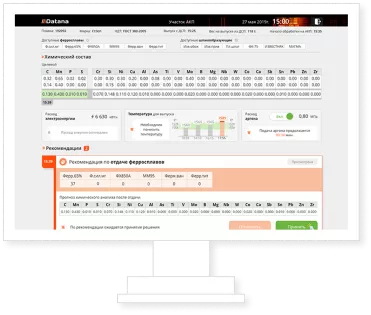
Range of issues
Increased costs for the steel production due to non-optimum ferroalloys consumption
Solution
Development and implementation of the solution with optimization model application, which calculates of the addition of the ferroalloys with minimum total cost, ensuring thereby the execution of production process and required physical and chemical parameters of the finished product.
- Reduction of the ferroalloys consumption by 3-7%
Control of purging with argon
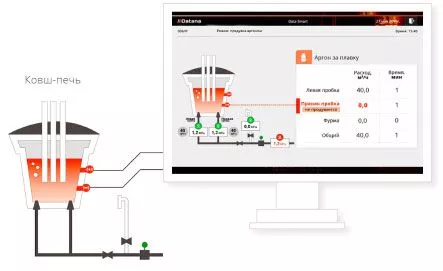
Range of issues
Increased content of the non-metallic inclusions in steel. Strong influence of the human factor on the process of purging with argon
Solution
System assess steel stirring intensity in real time and condition of each purging devices (plugs) based on the vibration readings. In case of deviation from the norms it provides recommendation on increasing/decreasing the argon supply.
- Increased steel quality
- Increased yield
How do we work

Production audit, target definition, tasks setting

Collection and analysis of the historical data

Models adjustment, interface adjustment

Tests, cost-benefit analysis

Additional functional capabilities

Integration with Automated System Control and controllers
IMPLEMENTATION EXPERIENCE
Reducing the costs for the ferroalloys at the Ladle-Furnace
Providing online recommendations regarding process management to the operators.Materials addition as per production costs criteria.
Has been implemented